About Admin
This author has not yet filled in any details.So far Admin has created 3 blog entries.
Reflecting on the Legislative Session that Ended in May 2022
Legislative efforts are a key membership benefit that ManufactureCT provides through our Government Affairs Committee. This committee is represented by: Jim Gildea, Chair Marcy Minnick, Co-Chair Kathy Saint, Jill Mayer, Kris Lorch, and Melissa Biggs. Each of them would like to thank the entire membership for your advocacy during this past Legislative Session. Here are the results:
In response to a membership survey sent out in November 2021, the GA committee decided to focus on four key issues:
1. Workforce Development:
- Expansion of Manufacturing Programs (Experiential Learning) in Public Schools
- Expansion of Manufacturing Programs (Precision Manufacturing, Mechatronics) in Technical High Schools
2. Energy: Electric Rates
3. Financial/Taxes: Expand R&D Tax Credits to S-Corps (currently available to C-Corps)
Workforce Development Highlights
- Participated in Congressman Jim Himes (CT-04) announcement that HCC has been awarded $1 million in federal funding to support the college's Advanced Manufacturing Technology Center in Bridgeport.
- Participated in and spoke at a community project funding for the New Haven Public Schools Manufacturing Program that brought $2 million into the system.
- Representatives of the ManufactureCT GA Committee spoke at the May Connecticut Technical Education and Career System Board meeting to discuss enhancing the Mechatronics program in our CT technical high schools.
Energy Highlights
- Met with Head of Commercial Energy Efficiency to discuss some programs they have and how it might help some of our members.
- Planned and Conducted a ManufactureCT Program Day wrapped around energy efficiency and potential Avangrid programs.
Financial/Taxes Highlights
- Encouraged our members to provide testimony on SB 351: An Act Expanding Research and Development Tax Credits to Pass Through Entities.
- Government Affairs Committee Submitted Written Testimony on SB 351 and provided virtual testimony.
- Government Affairs Committee Submitted Written Testimony combining SB98: An Act Expanding the Manufacturing Apprenticeship Tax Credit to Pass Through Entities and HB5488 An Act Expanding Expanding Research and Development Tax Credits to Pass Through Entities.
We are pleased to report that this advocacy paid off.
Both SB98 and SB351 were passed this session!
Both SB98 and SB351 were passed this session!
You can learn more about this ongoing work by accessing the full report HERE or by visiting the Government Affairs page of our website.
Connecticut Learns the Art of Regional Collaboration to Support Manufacturing
Our state is small but a powerhouse when it comes to manufacturing. A lot of similar things go on around the state, but each region is unique. The following summarizes an event held by ManufactureCT in March 2022. According to a CT Office of Workforce Strategy representative, "This is a really important time to do a presentation like this."
These events are free for Members. Find out more about our Membership benefits for manufacturers.
What are RSPs?
Regional Sector Partnerships (RSPs), sometimes called Manufacturing Sector Partnerships (MSPs), have been around for a while in Connecticut, with varying levels of awareness around the state. They're designed to help ecosystems leverage and sync up existing resources, creating stronger networks among complex landscapes of organizations and support structures. The concept and term has been in use nationally for about 30 years, and is enjoying a moment of popularity and centrality to the discussion of how to solve common problems in our state.
Why think regionally?
There is a logic to bringing together companies and businesses within a similar industry like manufacturing (or health care, agriculture, technology, etc.) at the regional level. States will always have a role to play, but the regional unit of implementation does become important when trying to get things done quickly and bring benefits to nearby workers and communities. Within RSPs, the work gets done in people's own backyards.
Members of RSPs mobilize together to tackle issues they cannot tackle individually. At the same time, they are more nimble than states. Specific issues vary region to region. Workforce is the "pound the table" issue of the moment. How are manufacturers directly connecting in a coordinated fashion with educational institutions and economic development organizations? The regional level seems to be reasonable, feasible, and of high value relative to the cost and other inputs to implement.
When did this movement start?
Connecticut started getting serious about these partnerships a few years ago. Since then, there's been lots of evolution and change and lessons learned. We started naming the need for regional units of implementation before Covid. Next Gen Sector Partnership was brought in to work with those regions for a set period of time, in this case a year and a half. State agencies and systems, along with statewide organizations, all contribute to this partnership model.
What is the problem that RSPs are attempting to solve?
Access to quality jobs is essential to communities. Local employers struggle to find the right talent to enable their businesses to grow and thrive. Programs exist, but often operate in separate silos. Some employers get over-solicited and overwhelmed by requests for their input, while others are ignored, skewing survey samples. Narrowly-defined topics can force conversations along certain predetermined paths, blocking partnerships from considering broader opportunities.
What does the model look like?
Instead of pushing out information, the intent of this is to create a pull to address actual needs. RSPs put industry at the center, where leaders can define and cham[ion their own agendas. Public partners sit around the outside of the room in listening mode.They give the floor to industry, and stay ready to help.
Anything business leaders agree is important becomes a priority. Partners work together to respond to industry needs. It's not about special initiatives, it's a way of collaborating and growing as a region. Creating more people with better jobs. In most communities, that's what matters most.
What are some examples in Connecticut?
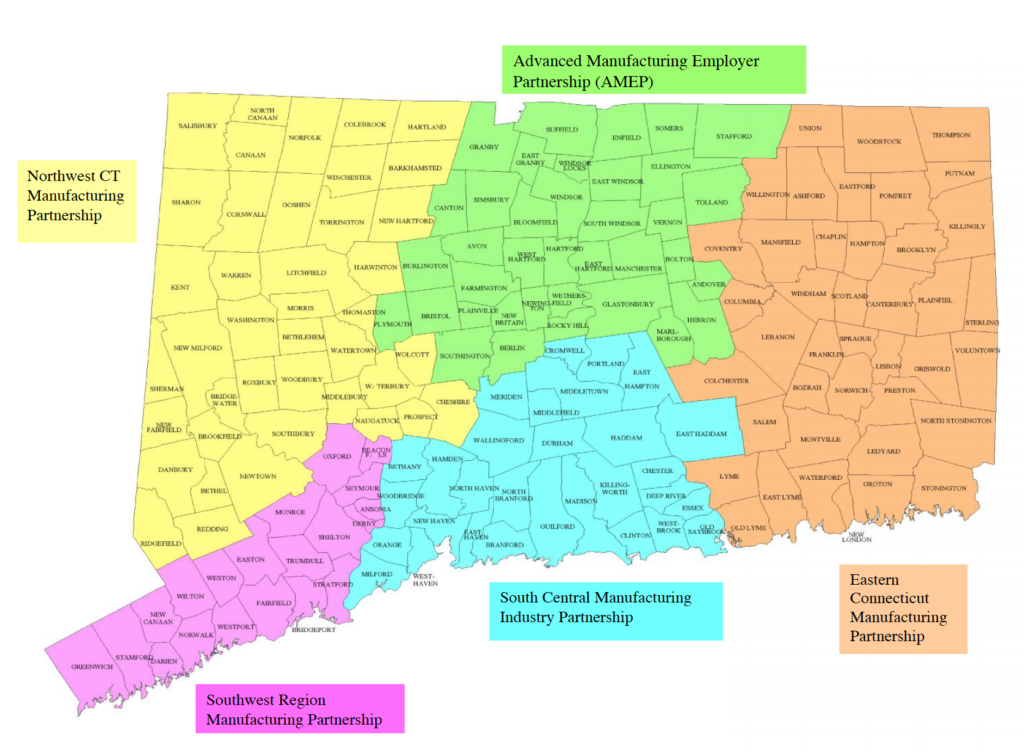
Southwest CT – People think of it as Connecticut's Gold Coast, but there are also upwards of 400 manufacturers, in a mixture of defense, high-tech, and other sectors. There is an increasing buzz around funding and programs, but senior leaders know that mobilization of resources must be strategic and measurable to be effective. They are focused on membership growth through regular communications, and engaging young professionals.
South Central CT (New Haven & Middlesex Counties) – It is perhaps Connecticut's most diverse area, so they are focused on Diversity, Equity, and Inclusion initiatives to bring more people into the manufacturing sector. They have invested lots of time up front so they can bring people on board at a pretty fast pace when they're willing to collaborate. Institutional relationships between schools, not for profits, and for-profit companies are important.
Eastern CT – This region now has a robust plastics industry, after diversifying from dependence upon Electric Boat. Universities helped to build a manufacturing pipeline initiative. The area is not heavily populated, and most things are a huge lift. Proactive action plans and extensive employer-led dialogue are making the difference. A recently-created training program has had 2000+ job placements, 80% of whom had no prior experience. They continue to have 60-70 applicants per week coming in, with 250 employers choosing to hire out of this program.
North Central CT – This region has been working together in one way or another for 9 or 10 years. Not duplicating efforts is important. They like to spot gaps and attempt to add value to our industry. Focus is on training and awareness through STEAM education programs, school counselors, parents, and all the other stakeholders to help youths make decisions about a future that includes manufacturing. They also have a support role in B2B matchmaking services.
Northwest CT – This RSP, like some of the others, is focused on raising awareness of manufacturing in all its diversity, and retaining more graduates in Connecticut so they can fuel advanced-level career tracks. Attracting manufacturing professionals from NY, MA, Northeast Corner ensures that reshoring continues and supply chains are strong. Growth areas are in specific markets like medical manufacturing, micro-machines, and electric vehicles, which all center on use of advanced technologies.
What are the common threads?
The bottom line across all of these RSPs, it seems, is keeping Connecticut businesses in Connecticut. ManufactureCT believes, along with the leadership groups in each of these regions, that the more voices we have the better solutions we can create. Let's all continue to engage and show everyone how much we want to stay involved, align with everything that's going on, and make it work!
Check out our new page about RSPs, with contact information about the speakers on this panel, who welcome questions and inquiries. This is just the first of many conversations about this timely and important topic.